MDC Mould, a pioneering company in the field of mould manufacturing, is making waves in the industry by revolutionizing the production of SMC (Sheet Molding Compound) Compression Fiberglass Reinforced Plastic (FRP) doors.
Innovating the Door Industry with SMC Technology
MDC Mould has been at the forefront of innovation in the manufacturing sector, and their latest venture into SMC Compression technology for FRP doors is setting new benchmarks. SMC, a composite material known for its exceptional strength and durability, is now being utilized to craft top-of-the-line doors under the expert guidance of MDC Mould.
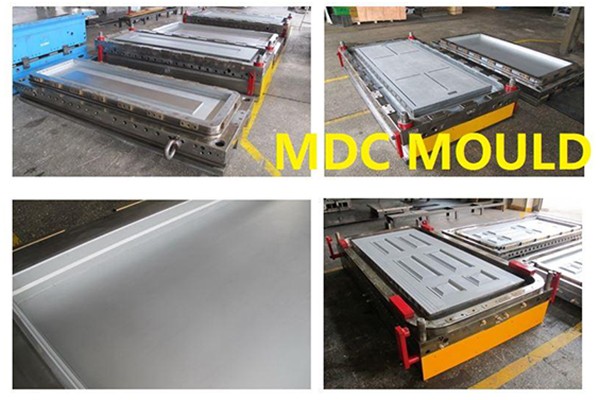
Precision, Strength, and Aesthetics
MDC Mould’s SMC Compression technology brings precision to the forefront of door manufacturing. Each door produced boasts unrivaled dimensional accuracy, ensuring a seamless fit into any architectural design. Beyond aesthetics, these doors are engineered for strength. They offer robust security while being remarkably lightweight, making them ideal for various applications, from residential to commercial.
Sustainable Solutions
MDC Mould is committed to sustainability, and this commitment extends to their SMC Compression FRP doors. The process minimizes material waste, ensuring eco-friendly production. These doors are built to last, reducing the need for frequent replacements and further contributing to environmental conservation.
Meeting Diverse Needs
The versatility of MDC Mould’s SMC Compression technology allows for the creation of doors that meet diverse needs. Whether it’s fire-rated doors for enhanced safety, soundproof doors for peaceful environments, or stylish doors for modern aesthetics, MDC Mould can tailor solutions to meet specific requirements.
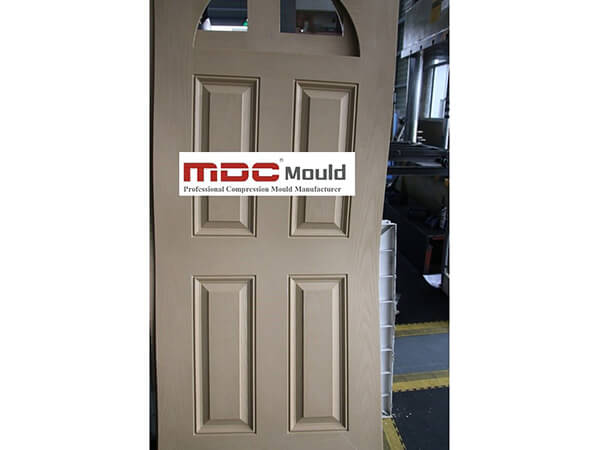
A Bright Future
As MDC Mould continues to push the boundaries of what is possible with SMC Compression technology, the future of door manufacturing is looking brighter than ever. Architects, builders, and homeowners can expect doors that not only meet industry standards but exceed them in terms of precision, strength, and sustainability.
MDC Mould’s foray into SMC Compression technology for FRP doors is a testament to their commitment to innovation and sustainability. Their doors combine precision engineering, strength, and aesthetics, offering a glimpse into the future of door manufacturing. As the demand for high-quality, eco-friendly doors grows, MDC Mould is well-positioned to lead the way with their revolutionary SMC Compression FRP doors.