Compression molding is a high-efficiency, cost-effective method for producing complex parts using composite materials. The molds used in this process—known as compression molds—are essential in ensuring quality, strength, and durability of the finished product. This article explores the main characteristics of compression molding molds, including their structure, materials, applications, and unique advantages.
1. Precision and Customization in Mold Design
Compression molding molds offer customization for various applications, such as automotive and industrial panels. They support:
- Custom Part Geometry: Tailored molds for complex shapes.
- Tolerance Control: Ensures precise part dimensions and reduces material waste.
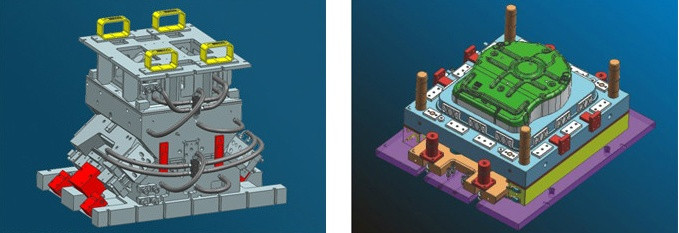
2. Materials for Compression Molding Molds
Compression molds are usually made from robust materials capable of withstanding high pressures and temperatures:
- Steel: Ideal for high-cycle durability.
- Aluminum: Great for lower-volume runs due to its thermal conductivity.
- Beryllium Copper: Used for intricate details and high thermal conductivity.
3. Mold Structure and Key Components
Key structural elements of compression molding molds include:
- Cavity and Core: Define the product shape.
- Heating System: Ensures material curing.
- Ejector System: Facilitates part release.
- Guiding System: Aligns mold halves for accuracy.
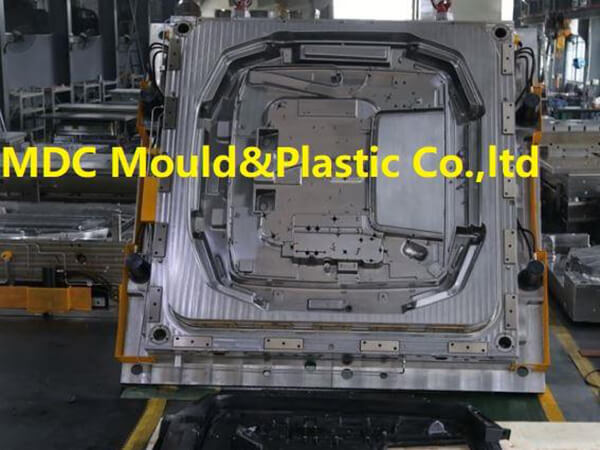
4. High Heat Resistance and Stability
Compression molds must withstand high temperatures for material curing, with features such as:
- Heat Resistance: Withstands up to 300°F or higher.
- Dimensional Stability: Retains shape under high temperatures and pressure.
- Even Heat Distribution: Reduces cycle times and ensures quality.
5. Durability and Longevity
Compression molds are designed for durability, often lasting thousands of cycles:
- Material Choice: High-quality steel and alloys enhance longevity.
- Surface Treatment: Chrome plating for wear resistance.
- Cycle Efficiency: Reduced wear compared to other mold types.
6. Cycle Time Efficiency
Efficient cycle times are essential for compression molding. Factors enhancing efficiency include:
- Quick Heat Transfer: High thermal conductivity materials reduce heating time.
- Optimized Part Release: Smooth finishes and ejector mechanisms minimize sticking.
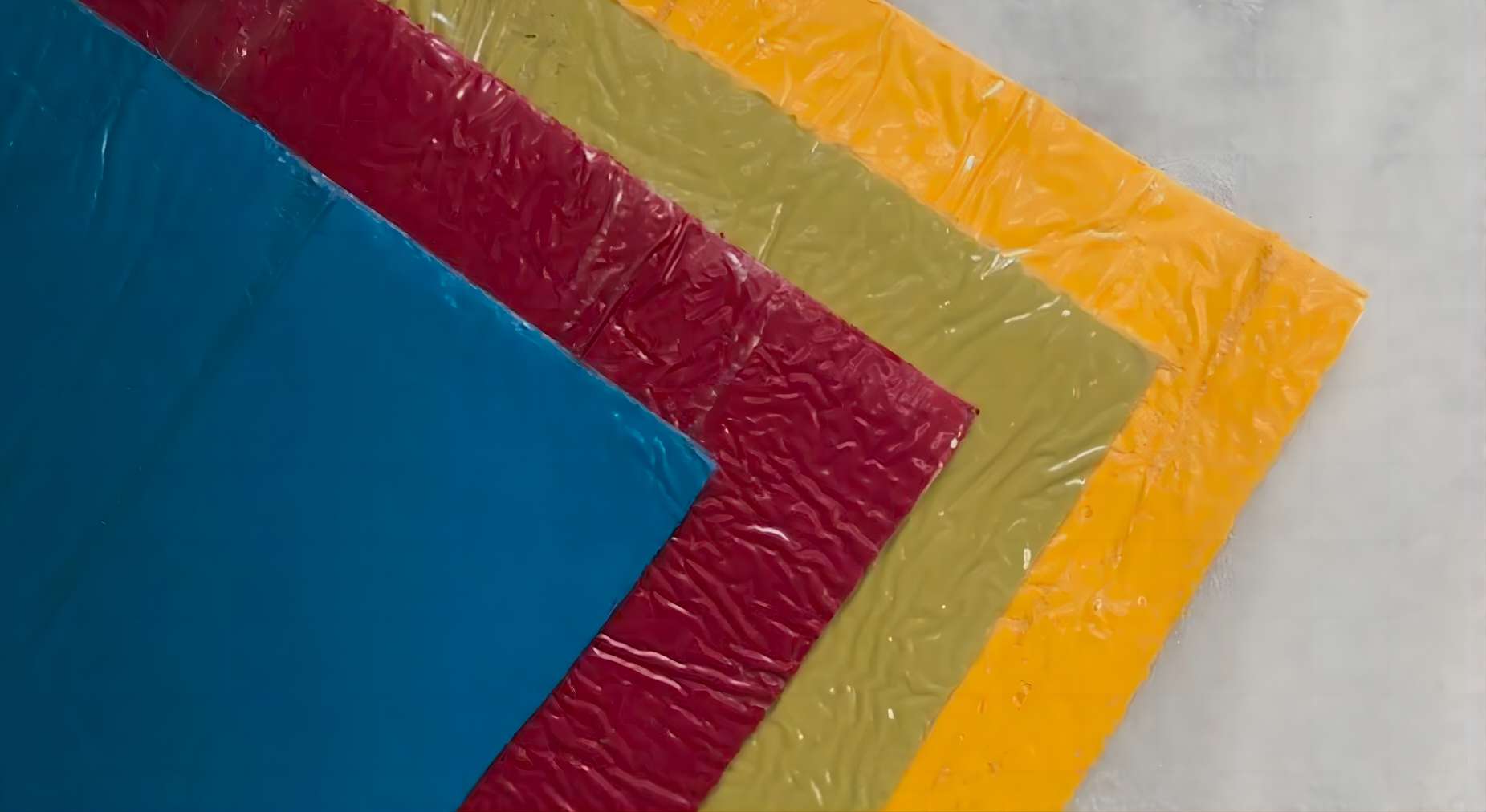
7. Compatibility with Composite Materials
Compression molds are compatible with a variety of composite materials like SMC, BMC, and thermosets:
- Material Flow: Even distribution for defect-free parts.
- Material Curing: Even curing for strength and durability.
8. Applications Across Diverse Industries
Compression molds are widely used in industries including automotive, aerospace, and electrical:
- Automotive: Panels, body parts, and interior components.
- Electrical: Insulators and housings with precise tolerances.
- Household Products: Durable components for daily use.
9. Cost-Effectiveness and Efficiency
Compression molding offers a cost-effective solution for medium to high-volume production:
- Low Material Waste: Pre-measured charges minimize excess material.
- Low Tooling Costs: Compared to injection molding.
- Simplified Setup: Reduces operational costs.
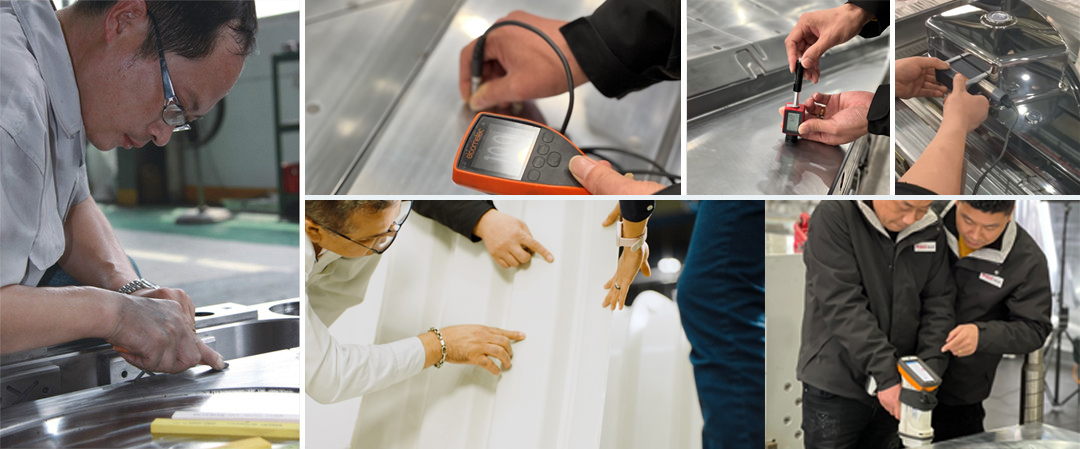
10. Design Flexibility and Enhanced Surface Finish
Compression molding molds offer flexibility and high-quality finishes:
- Texture and Pattern Integration: Custom finishes for aesthetic appeal.
- High-Quality Surface Finish: Smooth results, reducing post-processing needs.
- Minimal Draft Angles: More precise part geometries.
Conclusion
The characteristics of compression molding molds—durability, precision, and compatibility with composite materials—make them essential for high-quality production in diverse industries. These qualities not only ensure product durability but also optimize production efficiency. By understanding these characteristics, manufacturers can make informed decisions, improving product outcomes and achieving cost-effective, reliable manufacturing solutions.