The history of carbon fiber dates back further than many might realize. By the late 1800s, scientists were experimenting with carbon filaments for incandescent light bulbs. Less than a century later, these fine filaments paved the way for a future material: carbon fiber.
Today, carbon fiber is a critical component in many industries. It’s lightweight, strong, and heat-resistant, making it ideal for sensitive applications such as medical devices. However, as with any material, carbon fiber parts are best when manufactured correctly.
Planning to produce carbon fiber products? Before you do, here are three expert tips that will help you handle carbon fiber parts effectively.
1. Ensure Carbon Fiber is Ideal
First and foremost, ensure that carbon fiber is the right material for your application. It excels in many solutions, from prosthetics to aerospace-grade components. However, like any material, it’s not suitable for every job on the planet.
Carbon fiber boasts unparalleled tensile strength, being four times stronger than steel. Yet, its compressive strength is one of the few areas where it falls short of steel. For example, when used in submersibles, it might bend and collapse under pressure.
Ensure your carbon fiber product is not better served by other composites.
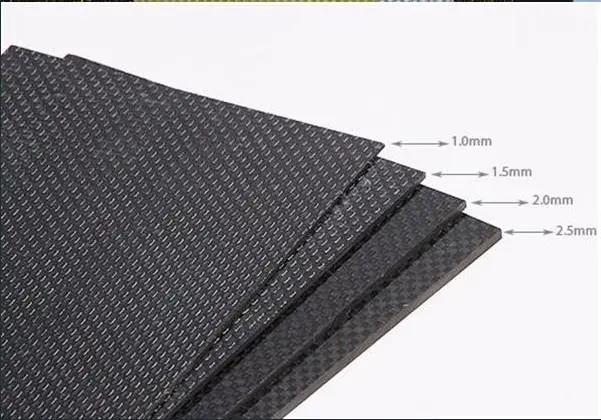
2. Use the Appropriate Fiber Grade
There isn’t a one-size-fits-all carbon fiber. Thicker, heavier fibers naturally create stronger, denser, and stiffer weaves. Finer fibers can form ultra-light finishes and covers.
Professionals categorize carbon fiber into three main aspects:
- Grade
- Weight
- Strength
For instance, something like a 5.6-ounce twill weave carbon fiber provides a classic carbon fiber look. For heavy industrial applications, you’ll need to increase the weight and grade accordingly.
Choosing the right epoxy resin will also affect the final physical properties of the carbon fiber. In many applications, you’ll need to bond the fibers together with something like cyanoacrylate adhesive. For thicker weaves, epoxy resin is necessary to keep the carbon fiber layers aligned and further enhance strength.
3. Properly Handle Carbon Fiber Parts
The beauty of carbon fiber is that it’s not rocket science to manufacture or use. That said, it doesn’t mean you can build it in your garage with just any parts at hand. Composites are tough and require sturdy tools for molding and cutting.
For example, cutting laminates works best when using carbide or diamond-coated tools. Carbon fiber is inherently abrasive and can quickly wear down steel scissors and razors.
Additionally, carbon fiber can produce dust during manufacturing and cutting. While this dust is non-toxic, it can be irritating to the lungs, eyes, and skin. You should wear a mask and goggles, just as you would when handling fiberglass.
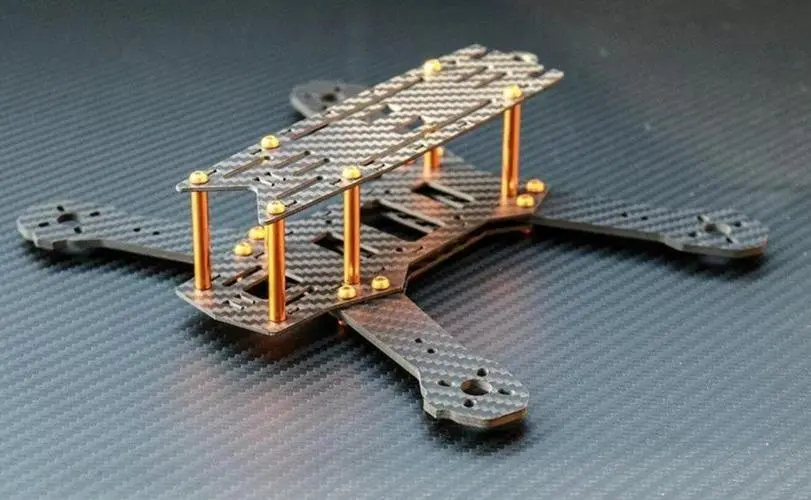
Conclusion
Carbon fiber molding and carbon fiber mold techniques require attention to detail and proper handling to ensure optimal performance. By confirming the suitability of carbon fiber for your application, selecting the right fiber grade and epoxy, and using the correct tools and safety measures, you can maximize the benefits of this remarkable material.