SMC and BMC, They are just like twins.
They are both a kind of resin mixture, which will be made into semi-finished products before molding. But at this time, BMC is made into clumps, while SMC is made into matte flakes, which are then cut to size.
The production process of SMC mold and BMC mold is also different. SMC molds are usually formed by compression molding, while BMC molds can be formed by different forming ways like injection, compression molding or transfer molding. These methods can all meet the production needs of medium and high volume.
Although the raw materials of SMC and BMC are roughly the same, there are differences in the use of glass fiber between the two materials. Glass fiber reinforced materials added to SMC generally account for up to 30%, and the fiber length is usually 25~50mm. In BMC, glass fiber reinforced materials generally account for 10%~30%, and the fiber length is usually 6~24mm. In comparison, the length of glass fiber used in SMC is longer than that used in BMC. Therefore, there are some differences in performance between these two. In general, SMC mold is stronger than BMC mold. In BMC molds, mineral fillers have a higher specific gravity and thus lower cost.
The advantages of SMC mold:
●Lightweight and high strength: With the same volume of materials, SMC is lighter than steel and aluminum, and its relative density is generally 1.3~2.0g/cm3, only 1/4~1/6 of ordinary steel, and 1/3 lighter than aluminum alloy. It can achieve the goal of lightweight, and has good impact resistance and energy absorption, and has high tensile strength, bending strength and impact toughness.
●High degree of integration and large degree of design freedom: The flow characteristics and molding process of SMC materials determine that many parts can be molded at one time, which can reduce the number of molds, tooling and the number of steps in the welding, assembly and other processes, thereby significantly reducing costs and realizing low-cost actions for low-volume components.
●Strong corrosion resistance: SMC material itself is a corrosion-resistant material, so it does not need phosphating treatment for anti-corrosion and improved bonding performance. Compared with metal, the application of SMC mold can reduce cost and save energy.
●Excellent heat resistance and paintability: SMC products have good heat resistance. After demoulding, SMC products can maintain dimensional stability at -50-200°C. Excellent heat resistance makes it suitable for use in auto parts. In addition, SMC material is the most suitable material for steel plate spraying technology. SMC has a thermal expansion coefficient and heat resistance similar to steel, and the sprayed SMC products can be cured at the same oven temperature as steel.
●Easy molding process: The molding of SMC molds mainly adopts metal-to-mold compression molding at present. The process is relatively simple. Cut the SMC sheet into the required shape and determine the number of layers to be added, then remove the protective film on both sides, stack it according to certain requirements, and place it on the appropriate position of the mold. Then it can be heated and pressurized according to the specified process parameters.
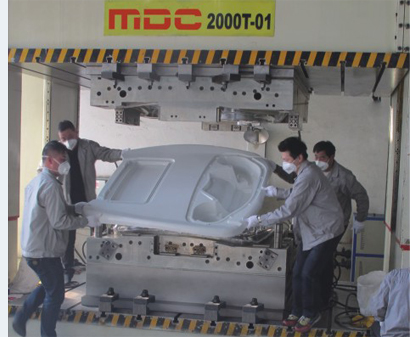
The advantages of BMC mold:
●Dimensional stability: The coefficient of linear expansion of BMC is smaller than that of ordinary thermoplastics, which makes BMC mold have high dimensional stability and dimensional accuracy.
●Good resistance to water and solvents: BMC has good corrosion resistance to water, ethanol, aliphatic hydrocarbons, grease and oil. Meanwhile, BMC has low water absorption, and its insulation performance is still good after soaking for one day.
●High heat resistance: The heat distortion temperature HDT of BMC is 200~280°C, and it can be used at 130°C for a long time.
●Aging resistance: BMC mold has very good aging resistance. It can be used indoors for 15-20 years, and its strength retention rate keeps above 60% after 10 years of outdoor exposure.
●Excellent electrical performance: Excellent arc resistance is the most outstanding advantage of BMC, which can reach about 190s.
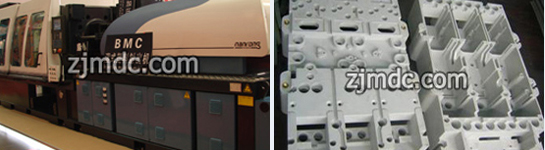
In general, when the requirements for the mechanical properties of the products, including tensile strength, bending strength and impact strength, etc. are higher; when the requirements for the surface area of the products is larger, and when the requirements for the lightweight of the products is higher, SMC will be selected.
In general, the requirements for the mechanical strength are lower than SMC but the cost need to stay low; when the requirements for the electrical properties and flame retardant properties of the products are higher; or when the requirements for the surface area of the product itself is small, people usually choose BMC.
MDC mould is a professional supplier of SMC and BMC materials. Based on the concept of taking technology as the guide and quality as the core, we will provide the best material for your project and provide the most reasonable solution. If your project needs to use SMC material or BMC material, please contact us. We can meet your need.