Carbon fiber mold making is a crucial process in composite manufacturing, widely used in the aerospace, automotive, marine, and sporting goods industries. A high-quality carbon fiber mold making kit includes all the necessary materials to create durable, lightweight, and precise composite molds.
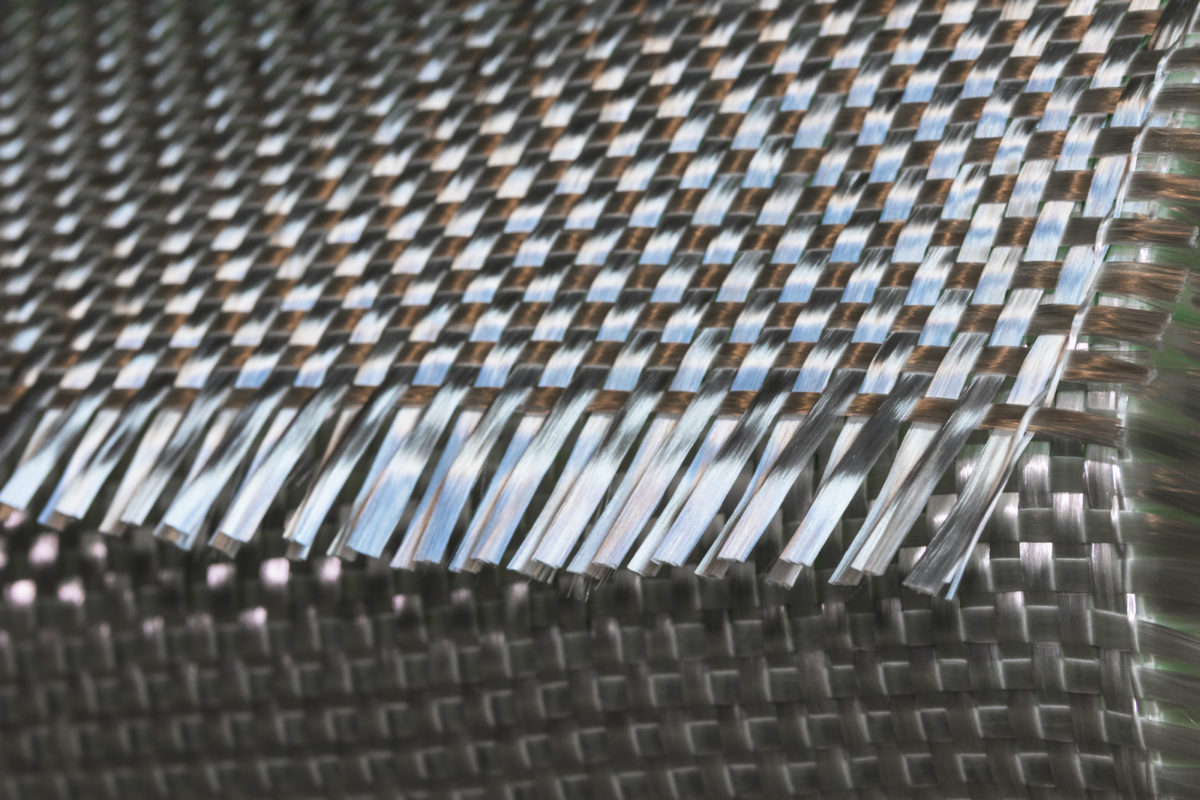
Why Use Carbon Fiber for Mold Making?
1. High Strength-to-Weight Ratio
Carbon fiber molds are lighter yet stronger than traditional metal molds, making them ideal for precision composite production.
2. Superior Heat Resistance
Carbon fiber materials exhibit excellent thermal stability, minimizing expansion or warping under high temperatures.
3. Long-Lasting Durability
Unlike metal molds, carbon fiber molds resist corrosion, wear, and chemical damage, increasing their lifespan.
4. Smooth Surface Finish
Carbon fiber molds provide high-gloss surfaces, reducing post-processing time and enhancing the final product’s appearance.
What’s Included in a Carbon Fiber Mold Making Kit?
Component | Function |
---|---|
Carbon Fiber Fabric | Provides structural reinforcement. |
Epoxy Resin System | Binds carbon fiber layers and ensures a strong, durable mold. |
Mold Release Agents | Prevents mold sticking and eases demolding. |
Vacuum Bagging Materials | Ensures uniform pressure for an air-free, high-quality mold. |
Step-by-Step Guide to Making a Carbon Fiber Mold
Step 1: Prepare the Master Pattern
Ensure your master pattern is clean, smooth, and coated with a high-quality mold release wax to facilitate easy demolding.
Step 2: Apply a Gel Coat Layer
Applying a heat-resistant epoxy gel coat ensures a smooth and durable mold surface.
Step 3: Lay Up Carbon Fiber Layers
Cut carbon fiber sheets to fit the mold, apply resin, and layer them carefully to build thickness.
Step 4: Vacuum Bagging & Curing
Use a vacuum bagging system to eliminate air bubbles and achieve uniform resin distribution.
Step 5: Post-Curing & Finishing
After full curing, sand and polish the mold for a high-quality finish.
Best Practices for Carbon Fiber Mold Making
- Use twill weave for flexibility and plain weave for surface smoothness.
- Select high-performance epoxy resin for better durability.
- Ensure proper vacuum bagging for a defect-free mold.
- Use high-quality mold release agents to prevent sticking.
Applications of Carbon Fiber Molds
Carbon fiber mold making kits are widely used in:
- Aerospace industry – Manufacturing lightweight aircraft parts.
- Automotive sector – Producing custom body panels and components.
- Marine industry – Creating high-performance boat hulls.
- Sports equipment – Making bicycle frames, helmets, and more.
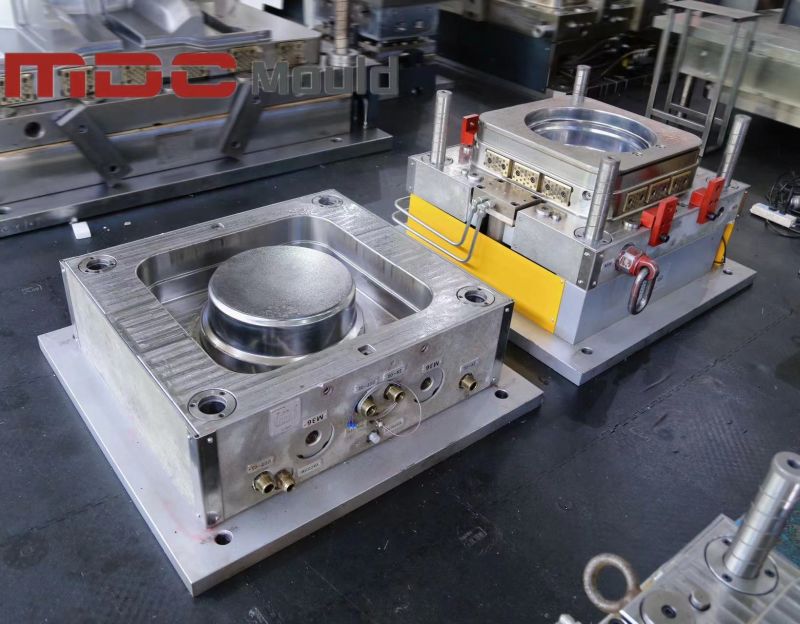
Conclusion
Using a carbon fiber mold making kit ensures high-quality, durable, and lightweight composite molds. Whether you’re working in aerospace, automotive, marine, or sports industries, investing in a professional-grade kit will significantly enhance your molding efficiency and precision.
Explore premium carbon fiber mold making kits today to start your journey into advanced composite manufacturing!