Composite materials have become essential in various industries, thanks to their exceptional strength-to-weight ratio, corrosion resistance, and design flexibility. From aerospace to automotive, the demand for lightweight, durable, and high-performance components has driven the evolution of composite mold casting techniques. To meet these industry needs, the use of a composite mold making kit has become increasingly popular, offering an all-in-one solution for creating high-quality molds.
What is Composite Mold Casting?
Composite mold casting is a process used to create complex shapes and forms from composite materials. These materials typically include reinforced plastics such as carbon fiber, fiberglass, or BMC (Bulk Molding Compound) used in BMC molding and BMC moulding. The mold defines the shape of the final product and is critical for the success of the compression molding process.
The quality of the mold directly impacts the quality of the final product, which is why precision in mold making is crucial. This process is widely used in industries such as thermoforming mould, thermoforming tooling, and thermoset mold production.
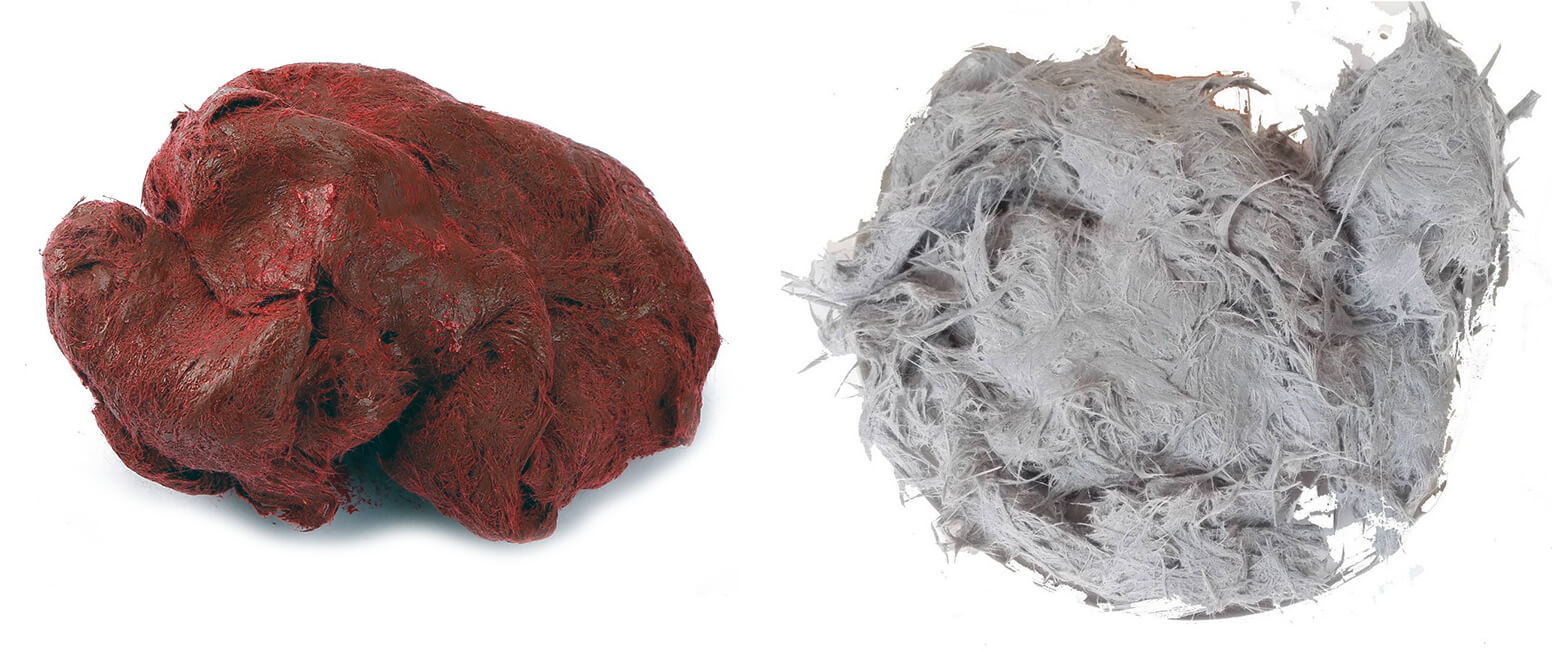
The Composite Mold Casting Process
- Mold Design and Fabrication: The first step is designing the mold, often using CAD software to create a precise model. Molds can be made from materials such as aluminum, steel, or even composites.
- Surface Preparation: The mold surface must be prepared to ensure a smooth finish on the final product, often involving the application of a release agent to prevent the composite material from sticking.
- Lay-Up Process: Layers of composite material, such as those used in SMC molds and composite molds, are placed into the mold to optimize the strength and stiffness of the final product.
- Curing: The mold is placed in an oven or autoclave to cure, solidifying the resin matrix and forming a rigid structure. This step is critical in composite molding and thermoforming mold processes.
- Demolding and Finishing: After curing, the part is carefully removed from the mold. Additional processes such as trimming, sanding, and painting may be applied to achieve the desired finish.
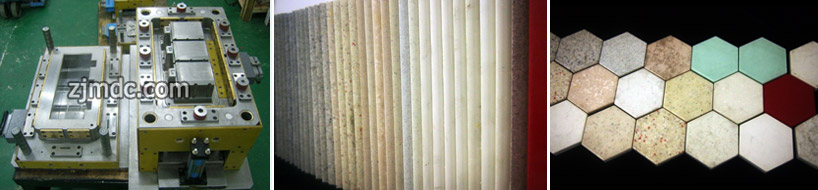
The Role of a Composite Mold Making Kit
A composite mold making kit is an invaluable resource, especially for professionals working with compression molds, thermoforming tools, or composite molds. These kits include all necessary materials and tools to create high-quality molds, streamlining the process and minimizing errors.
What’s Included in a Composite Mold Making Kit?
- Resins and Hardeners: Essential for creating the mold itself, these components ensure proper curing and durability, vital in thermoset molding.
- Reinforcing Fibers: Some kits include fibers like fiberglass to strengthen the mold, particularly in high-stress areas.
- Release Agents: These agents prevent the composite material from sticking to the mold during casting, ensuring easy demolding.
- Mixing Tools: Brushes, mixing cups, and stir sticks are included to help apply the resin and hardener accurately.
- Instructional Guides: Many kits provide detailed instructions or access to tutorials, making it easier for beginners to understand the mold-making process.
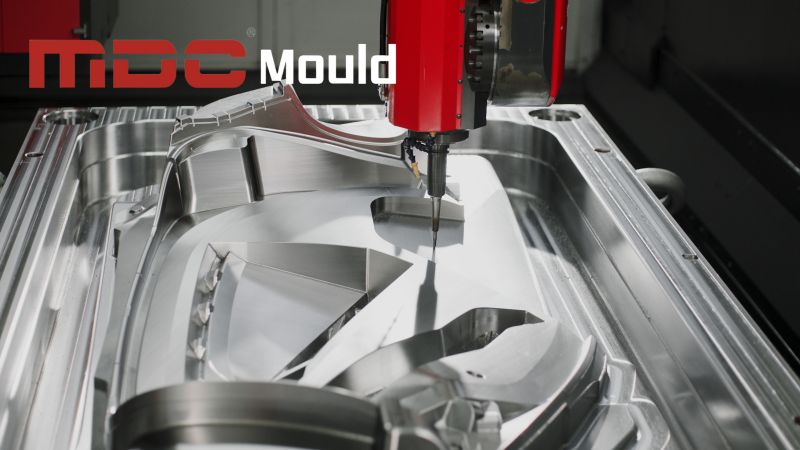
Benefits of Using a Composite Mold Making Kit
Using a composite mold making kit offers several advantages, particularly for those working in thermoforming tool and composite molding:
- Convenience: Kits offer a convenient solution by providing all necessary materials in one package.
- Cost-Effective: Purchasing a kit can be more affordable than buying each material individually, and it reduces the risk of buying incompatible products.
- Quality Assurance: Kits are typically designed by professionals, ensuring high-quality materials and compatibility.
- Time-Saving: The mold-making process is expedited with all materials readily available, reducing preparation time.
Applications of Composite Mold Casting
Composite mold casting has a wide range of applications across various industries:
- Aerospace: Used to create lightweight, strong components like aircraft wings and fuselage sections.
- Automotive: Essential for producing parts like bumpers and dashboards, where weight reduction is crucial.
- Marine: Composite materials are used to create boat hulls and decks, offering excellent corrosion resistance.
- Sports Equipment: Composite materials are favored for their strength and lightweight properties in products like tennis rackets and bicycle frames.
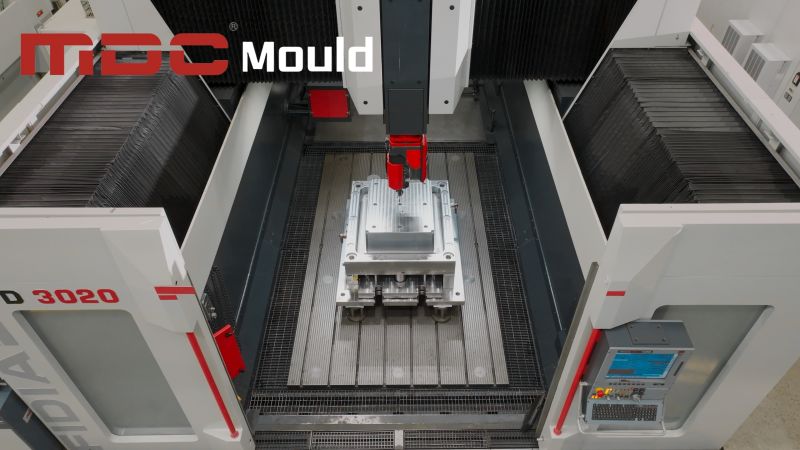
Conclusion
Composite mold casting is a sophisticated process vital to manufacturing high-performance components across various industries. Utilizing a composite mold making kit streamlines the process, offering a comprehensive solution that saves time, reduces costs, and ensures the production of top-tier molds. Whether you’re working with SMC molds, thermoforming molds, or thermoset molds, mastering the art of composite mold casting with the right tools is essential for success.
1 вин официальный https://1win7019.ru/ .