Superior Insulating Properties
One of the most significant advantages of SMC meter boxes over metal counterparts is their excellent insulating properties. Unlike metal, SMC does not conduct electricity. This non-conductive nature provides a crucial safety benefit:
- Safety: SMC meter boxes do not pose an electrical hazard when touched by a live wire. This reduces the risk of electric shock, making them safer for both installers and end-users.
- No Grounding Required: Because they are non-conductive, SMC meter boxes do not need to be grounded. This simplifies the installation process, saving both time and money.
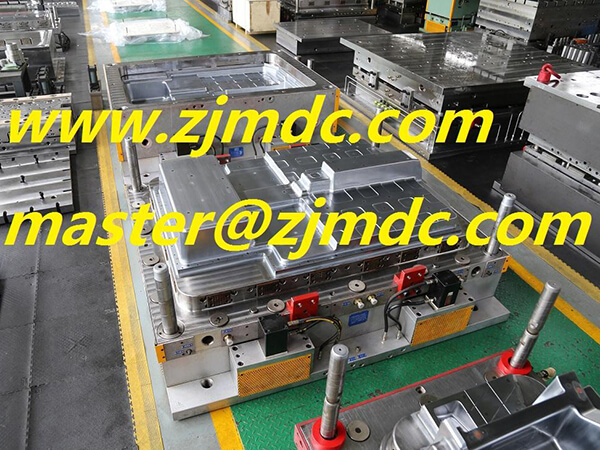
Cost-Effectiveness and Ease of Installation
SMC meter boxes offer significant cost advantages over both metal and traditional plastic options. Here’s how:
- Material Costs: SMC is generally less expensive to produce than metal, and it offers a better performance-to-cost ratio than many plastics.
- Lightweight: SMC is much lighter than metal, which makes the meter boxes easier to handle and install. This reduces labor costs and minimizes the risk of injury during installation.
- Ease of Manufacturing: SMC can be molded into complex shapes with high precision, allowing for the integration of various features into a single part, which reduces assembly time and costs.
High Mechanical Strength and Durability
One of the key reasons for the popularity of SMC in meter box manufacturing is its high mechanical strength and durability:
- Resistance to Stress and Impact: SMC has high tensile strength, meaning it can withstand significant stress without cracking or breaking. This makes it suitable for outdoor applications where it may be exposed to harsh conditions.
- Long Lifespan: The robust nature of SMC ensures that meter boxes have a long service life, reducing the need for frequent replacements and maintenance.
Fire Resistance and Safety
Fire safety is a critical consideration for any electrical enclosure, and SMC excels in this area:
- Self-Extinguishing Properties: SMC can be formulated to be self-extinguishing, which means it will not catch fire easily and can prevent the spread of flames in the event of a fire. This property is especially important for electrical applications where the risk of fire is a concern.
- Thermal Stability: As a thermoset plastic, SMC does not melt at high temperatures. This characteristic enhances the safety and integrity of the meter box in extreme conditions.
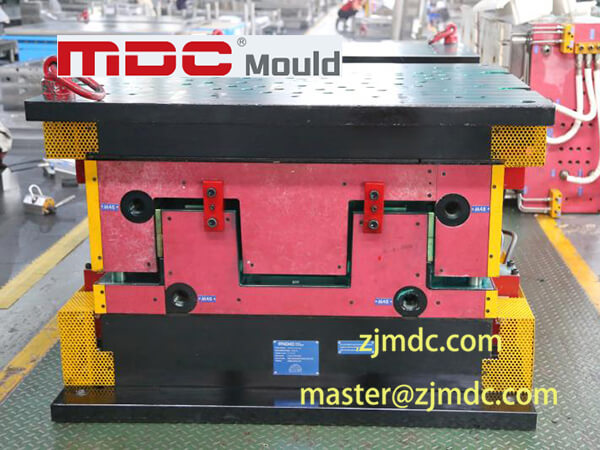
Thermal Stability
In addition to its fire resistance, SMC’s thermal stability provides further benefits:
- High Temperature Tolerance: SMC mold can withstand high temperatures without deforming or losing its mechanical properties. This makes it ideal for use in environments where it may be exposed to heat.
- Consistency in Performance: The material’s stability ensures that it maintains its performance characteristics over a wide range of temperatures, providing reliable protection for the electrical components housed within the meter box.
Manufacturing Process of SMC Enclosures
To better understand the advantages of SMC meter boxes, it is helpful to look at the manufacturing process. MDC, a leader in SMC enclosure mold manufacturing, demonstrates the efficiency and precision of this process.
- Material Preparation
- Compounding: SMC is created by combining resin, fillers, and reinforcement materials, such as glass fibers, into a dough-like compound. This mixture is then rolled into sheets.
- Storage: The SMC sheets are stored and allowed to mature, which helps to achieve the desired consistency and properties for molding.
- Molding Process
- Mold Setup: The matured SMC sheets are placed into a heated mold cavity.
- Compression Molding: The mold is closed, and heat and pressure are applied. The SMC material flows to fill the mold cavity, taking on the desired shape. This process ensures high precision and the ability to produce complex geometries.
- Curing: The heat initiates a chemical reaction that cures the SMC, transforming it into a rigid, solid form. The curing process ensures that the molded part has the desired mechanical and physical properties.
- Finishing
- Trimming and Drilling: After molding, the parts may require trimming of excess material and drilling of holes for mounting or other features.
- Surface Treatment: Depending on the application, the SMC meter boxes may undergo additional surface treatments to enhance their appearance or performance, such as painting or coating.
- Quality Control
- Inspection: Each meter box is inspected for defects and to ensure it meets the required specifications.
- Testing: Functional tests, such as impact resistance and electrical insulation tests, are conducted to verify the performance of the meter boxes.
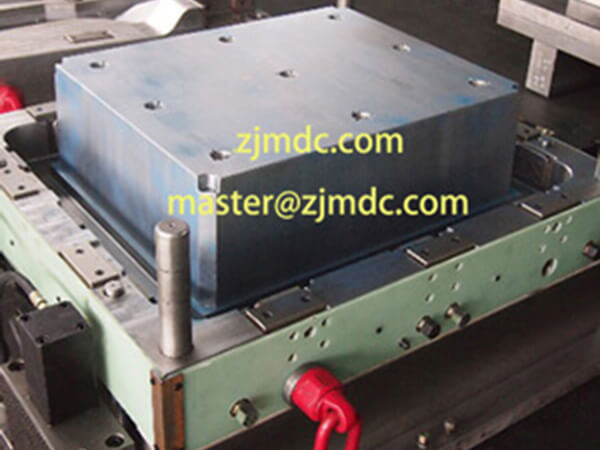
Conclusion
The shift from metal and traditional plastic to SMC for meter box manufacturing is driven by the numerous advantages SMC ( composite mold ) offers. Its superior insulating properties, cost-effectiveness, ease of installation, high mechanical strength, fire resistance, and thermal stability make SMC meter boxes an ideal choice for modern electrical enclosures. The precision and efficiency of the SMC manufacturing process further enhance these benefits, ensuring high-quality, durable products. As a leader in SMC enclosure mold manufacturing, MDC exemplifies the capabilities and advantages of this innovative material, setting a standard for safety, reliability, and performance in the industry.
buy generic misoprostol over the counter – buy misoprostol 200mcg online purchase diltiazem pill