Discover the key factors that influence compression molding cycle time and how to optimize production efficiency.
Understanding the Compression Molding Cycle
Compression molding consists of multiple stages, each impacting the total processing time. From material preheating to curing and cooling, every step plays a crucial role.
- Preheating the Material: 30 seconds to 5 minutes depending on material.
- Loading the Mold: 5 to 20 seconds.
- Compression and Forming: 30 seconds to several minutes.
- Curing or Cooling: 1 to 10 minutes for thermosets, 30 seconds to 5 minutes for thermoplastics.
- Mold Opening and Part Removal: 5 to 15 seconds.
- Trimming and Post-Processing: 1 to 5 minutes if required.
Factors Affecting Compression Molding Time
Several factors influence the cycle time of compression molding:
Material Type
Different materials require varying processing times:
- SMC (Sheet Molding Compound): 2-5 minutes
- BMC (Bulk Molding Compound): 1-3 minutes
- Rubber Compression Molding: 5-15 minutes
- Carbon Fiber Composites: 10-20 minutes
Part Thickness and Complexity
Thicker and more complex parts require longer curing times. A 3 mm thick part may cure in 2 minutes, while a 10 mm thick part may take 7 minutes.
Mold Temperature and Pressure
Higher mold temperatures and pressure settings reduce cycle time by ensuring efficient material flow and faster curing.
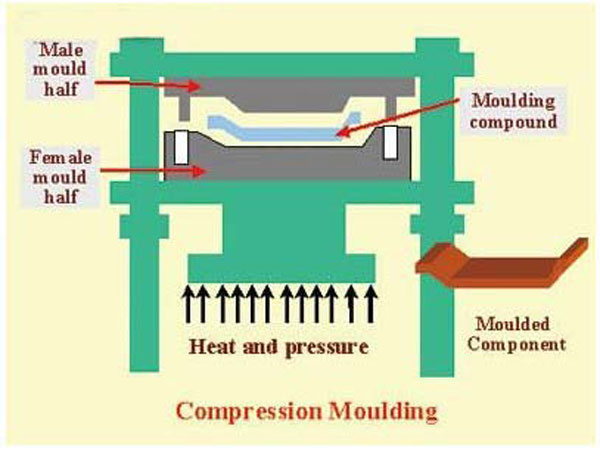
Optimizing Compression Molding Time
- Use fast-curing materials to shorten cycle times.
- Optimize mold temperature and pressure settings for better efficiency.
- Improve mold design with heated molds and proper venting.
- Implement automation for material handling and ejection.
Typical Compression Molding Cycle Times by Industry
Industry | Material | Cycle Time |
---|---|---|
Automotive | SMC, BMC | 1-5 minutes |
Aerospace | Carbon Fiber Composites | 10-20 minutes |
Electrical | BMC, Phenolic Resins | 1-3 minutes |
Consumer Goods | Rubber, Thermoplastics | 3-10 minutes |
Conclusion
Compression molding cycle time depends on material type, part complexity, curing requirements, and process optimization. By selecting the right materials, optimizing mold conditions, and incorporating automation, manufacturers can enhance efficiency and reduce costs.
For high-quality compression molded parts, understanding these key factors is essential to achieving faster production cycles.
продвинуть сайт самостоятельно
накрутка поведенческих факторов сайта