Introduction to Carbon Fiber Manufacturing Processes
Carbon fiber is a high-performance composite material known for its exceptional strength, light weight, and versatility. It is widely used across industries, from automotive to aerospace, due to its impressive mechanical properties. The two primary methods of carbon fiber manufacturing are wet carbon fiber and dry carbon fiber, each offering distinct benefits and applications. Understanding the differences between these processes is key to selecting the most appropriate method for your specific manufacturing needs.
1. Wet Carbon Fiber: What Is It and How Does It Work?
Wet carbon fiber, also known as resin-infused carbon fiber, involves the manual impregnation of carbon fiber cloth with epoxy resin. The “wet” terminology stems from the fact that carbon fibers are manually “wetted” with resin before being placed into molds for curing. This process can be done through methods such as resin infusion or hand lay-up.
Process Overview
The typical process for manufacturing wet carbon fiber components includes:
- Manual Wetting: Carbon fiber is laid by hand and soaked with resin, either manually or using a vacuum-assisted resin infusion technique.
- Curing: The resin-saturated carbon fiber is then cured, typically in an oven or at room temperature.
- Final Product: Once cured, the component is removed from the mold and is ready for finishing and inspection.
Pros of Wet Carbon Fiber
- More cost-effective than dry carbon fiber methods, making it suitable for lower-volume production.
- Ideal for larger components where intricate detail and precision are less critical.
- Greater flexibility in terms of resin choice and curing speed, which benefits rapid prototyping.
Cons of Wet Carbon Fiber
- Lower precision due to manual handling, potentially leading to inconsistent resin distribution.
- Higher resin-to-fiber ratio, which can reduce the overall strength and durability of the component.
2. Dry Carbon Fiber: The High-Performance Alternative
Dry carbon fiber, or prepreg carbon fiber, is made by pre-impregnating carbon fibers with resin at the factory. Unlike wet carbon fiber, there is no need for manual resin application, as the fibers are already impregnated with resin. This process requires more specialized equipment, such as high-pressure autoclaves, to cure the components.
Process Overview
The dry carbon fiber manufacturing process follows these steps:
- Prepreg Carbon Fiber: Carbon fiber is impregnated with resin at the factory and stored at low temperatures to prevent premature curing.
- Molding: Prepreg carbon fiber is laid into molds, then placed into high-pressure autoclaves where it is cured under heat and pressure.
- Final Product: After curing, the part is removed from the mold and inspected for quality and performance.
Pros of Dry Carbon Fiber
- Produces stronger, more durable components due to a lower resin-to-fiber ratio.
- Highly consistent in terms of resin content and fiber alignment, which improves precision and reliability.
- Ideal for high-performance applications, including aerospace and automotive industries, where strength and precision are paramount.
Cons of Dry Carbon Fiber
- Significantly more expensive due to the need for specialized equipment and prepreg materials.
- Longer production times, as parts need to be cured in an autoclave under controlled conditions.
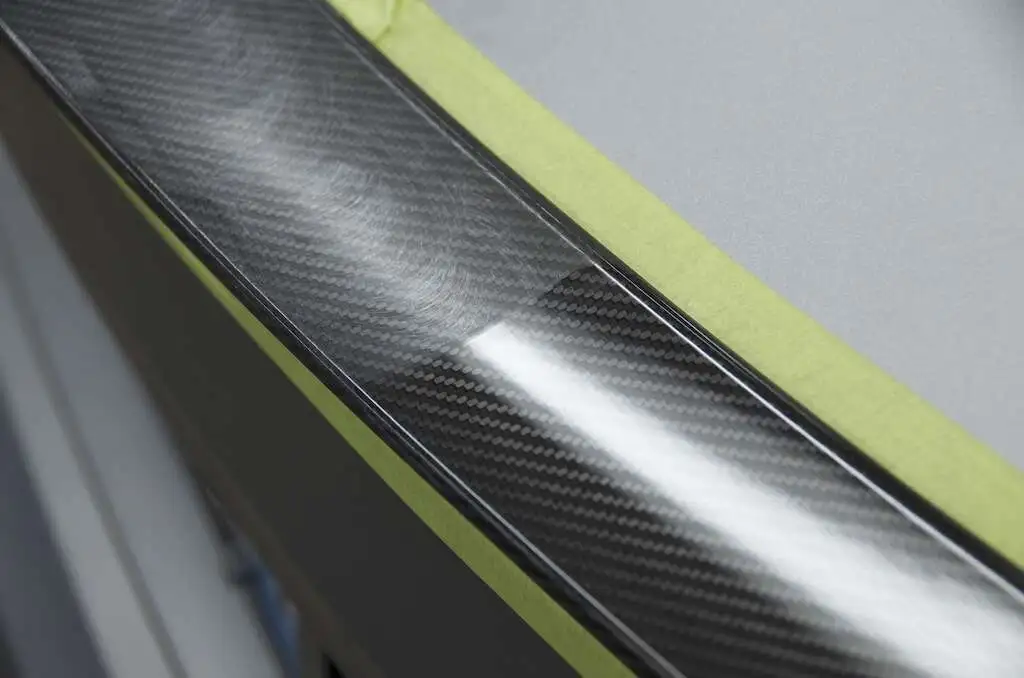
3. Comparing Wet and Dry Carbon Fiber: Which is Better?
When it comes to choosing between wet and dry carbon fiber, it’s crucial to consider the specific requirements of your project. Both methods have their place in composite manufacturing, but understanding their differences can help you make a more informed decision.
Aspect | Wet Carbon Fiber | Dry Carbon Fiber |
---|---|---|
Cost | Lower cost, ideal for low-volume production | Higher cost due to specialized equipment and materials |
Strength and Durability | Moderate strength, suitable for non-structural applications | Superior strength, ideal for high-performance components |
Precision | Lower precision due to manual processes | High precision and consistency in part manufacturing |
Production Speed | Faster, suitable for prototyping and small batches | Slower due to autoclave curing, ideal for mass production |
Applications | Non-critical parts like enclosures, panels | High-performance parts like aerospace components, automotive frames |
4. Compression Molding with Carbon Fiber: An Efficient Alternative
Another widely used method for producing carbon fiber parts is compression molding, which is ideal for high-volume production of composite molds. In this process, carbon fiber sheets (often prepreg materials) are placed in a heated mold, and pressure is applied to form the desired shape.
Benefits of Compression Molding
- Ensures uniform resin distribution and fiber impregnation, reducing the chances of defects.
- Highly efficient for mass production due to shorter cycle times compared to other methods.
- Suitable for creating complex shapes and designs, especially when combined with composite tooling.
Compression Molding vs. Wet and Dry Carbon Fiber
While compression molding can provide similar strength and precision to dry carbon fiber processes, it offers a more cost-effective solution for large-scale manufacturing. However, the level of detail achievable in compression molding may not be as high as that produced by dry carbon fiber techniques.
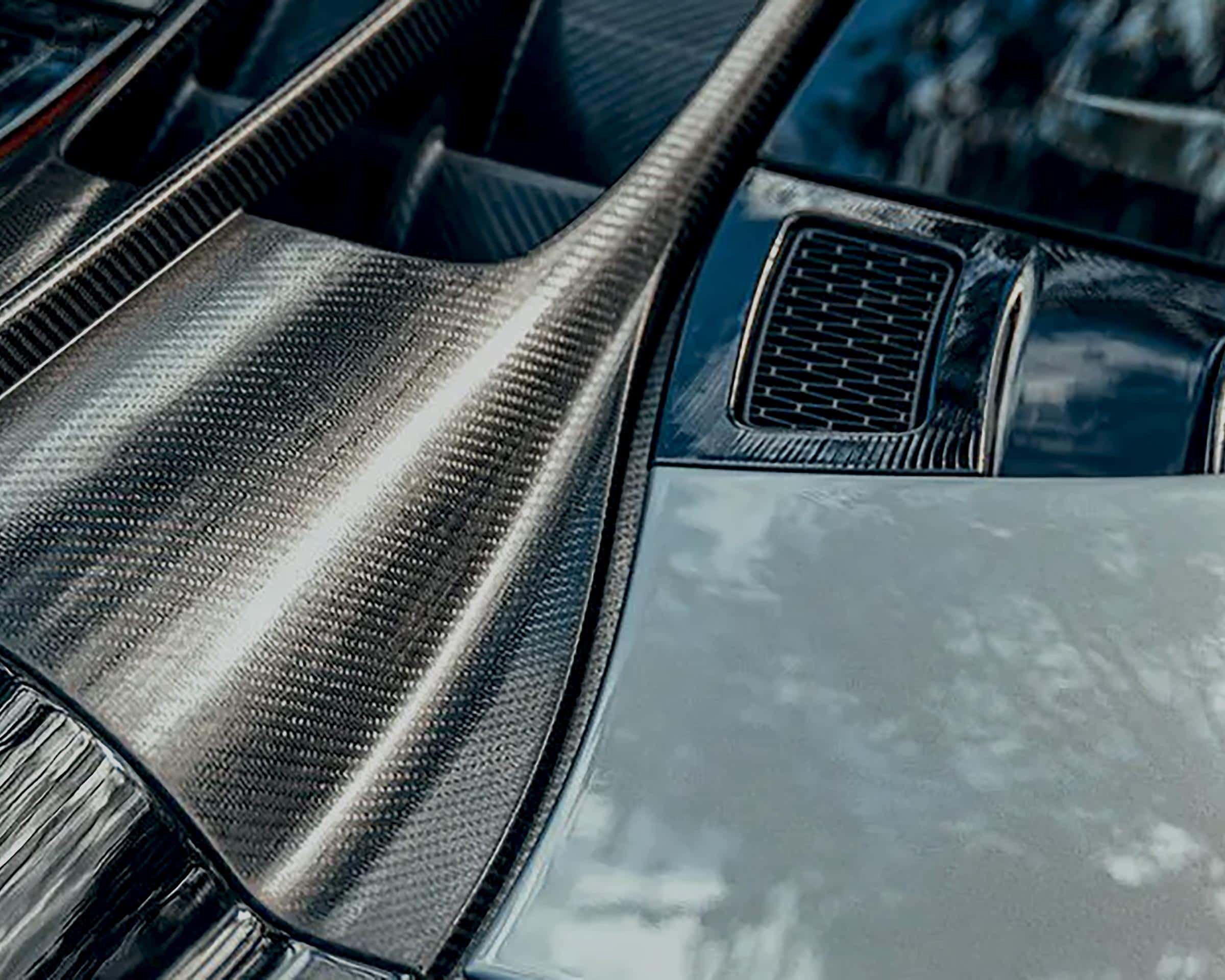
Conclusion: Choosing the Right Process for Your Carbon Fiber Components
The decision between wet and dry carbon fiber depends on your specific manufacturing requirements, including cost constraints, performance needs, and production scale. Wet carbon fiber offers a budget-friendly solution for larger components, while dry carbon fiber delivers superior performance for high-end applications. Additionally, techniques like compression molding provide an efficient alternative for mass production of carbon fiber components.
Whether you are looking to manufacture automotive parts, aerospace components, or consumer goods, understanding the differences between these carbon fiber processes and selecting the right one can ensure optimal results for your project.
улучшение рейтинга криптобиржи http://www.prodvizhenie-kriptovalyuta2.ru/ .