Learn about the features, processes, and uses of these two common industrial molding techniques.
What Is Isostatic Molding?
Isostatic molding uses pressure from all directions with a flexible mold and a pressurized medium (like water or oil). This makes sure the material is spread evenly and gets rid of air pockets, which is great for making strong parts with the same density throughout.
Features of Isostatic Molding
- Uniform pressure distribution across the material.
- Suitable for complex geometries and intricate shapes.
- Works well with ceramics, powdered metals, and advanced composites.
- Produces parts with high density and exceptional mechanical strength.
The Isostatic Molding Process
- Place powdered material into a flexible mold.
- Submerge the mold into a pressurized medium, such as water or oil.
- Apply uniform pressure to compact the material into shape.
- Remove the mold and sinter the part to enhance strength and durability.
Applications of Isostatic Molding
- Ceramic Parts: These parts are used in industrial and medical settings to make dense and precise ceramic components.
- Powder Metallurgy: This process is ideal for creating high-performance parts for the aerospace and automotive industries.
- Advanced Composites: These composites are used in critical applications where uniform density and strength are essential.
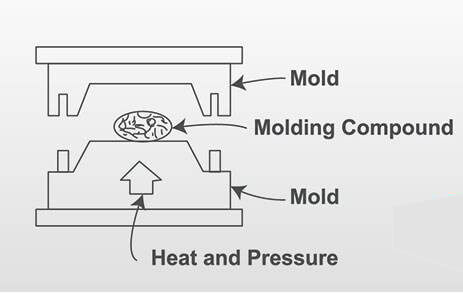
Understanding Compression Molding
Compression molding is a process where heated material is placed into a metal mold. The material is pressed together under high pressure and heat to form a specific shape. This process is cost-effective and suitable for large-scale production.
Features of Compression Molding
- Pressure is applied directly, typically from the top.
- Cycle times are short, making it efficient for mass production.
- It works with thermosetting plastics, rubbers, and composite materials.
- It can produce large quantities at a lower cost.
The Compression Molding Process
- Pre-heat the material and place it into a mold cavity.
- Apply pressure by lowering the mold to compress the material.
- Heat the material to make it harden and take the desired shape.
- Open the mold and eject the finished part.
Applications of Compression Molding
- Automotive Parts: Bumpers, dashboards, and interior trims.
- Electrical Components: Insulators and circuit breaker housings.
- Consumer Goods: Durable handles, containers, and other items.
Comparing Isostatic and Compression Molding
Aspect | Isostatic Molding | Compression Molding |
---|---|---|
Pressure Application | Uniform from all directions | Directional, typically top-down |
Materials Used | Powdered metals, ceramics, composites | Thermosets, rubbers, thermoplastics |
Product Characteristics | High density and uniformity | Durable and mass-producible |
Cycle Time | Longer due to sintering | Shorter for rapid production |
Choosing the Right Method
The choice between isostatic and compression molding depends on several factors:
- Material Requirements: Use isostatic molding for ceramics and powdered metals; compression molding for thermosetting plastics.
- Part Complexity: Isostatic molding excels in intricate designs, while compression molding suits simpler geometries.
- Production Volume: Compression molding is better for high-volume production due to shorter cycles.
- Cost Efficiency: Isostatic molding is more expensive but delivers superior quality for critical applications.
For expert guidance on molding techniques, contact us. Our team is ready to help you achieve optimal results for your manufacturing needs.
I am no longer positive the place you are getting your information, but great topic. I must spend a while studying more or figuring out more. Thanks for excellent info I was on the lookout for this information for my mission.