3D printing technology has rapidly transformed various industries, and one of the most exciting developments is the use of 3D printed carbon fiber molds in manufacturing. These molds offer a combination of precision, durability, and cost-effectiveness, revolutionizing processes in industries like aerospace, automotive, medical devices, and more. In this article, we’ll explore the advantages, applications, and future prospects of 3D printed carbon fiber molds, focusing on their impact on the molding industry.
What are 3D Printed Carbon Fiber Molds?
Carbon fiber molds are typically made by layering carbon fiber fabric and resin over a tool or model, and they are known for their high strength-to-weight ratio and resistance to deformation under high temperatures. With 3D printing technology, manufacturers can now produce these molds faster, with fewer manual processes and enhanced customization.
3D printed carbon fiber molds are created by using a blend of carbon fiber filaments within the 3D printing process. The carbon fiber filament is mixed with a thermoplastic resin, making the printed parts not only lightweight but also incredibly strong. This technology significantly speeds up mold production and reduces costs compared to traditional molding methods.
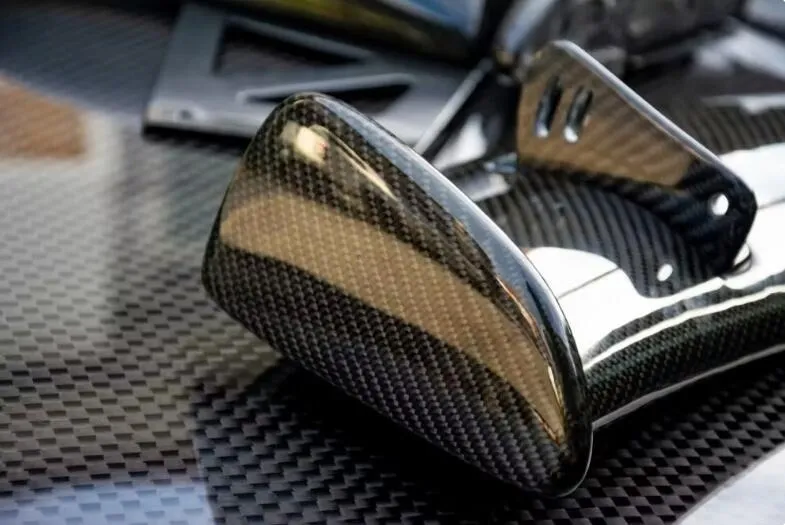
Advantages of 3D Printed Carbon Fiber Molds
- Speed and Efficiency: 3D printing dramatically reduces mold production time, allowing manufacturers to meet tight deadlines and iterate designs quickly.
- Customization and Design Flexibility: Complex geometries are achievable with 3D printing, allowing for highly customized molds.
- Cost-Effectiveness: 3D printed molds are cheaper for low-volume production due to reduced labor and material costs.
- Lightweight and Durable: Carbon fiber’s lightweight properties and high strength make 3D printed molds easy to handle and long-lasting.
- Environmental Benefits: Reduced material waste and energy consumption make 3D printed molds an eco-friendly option.
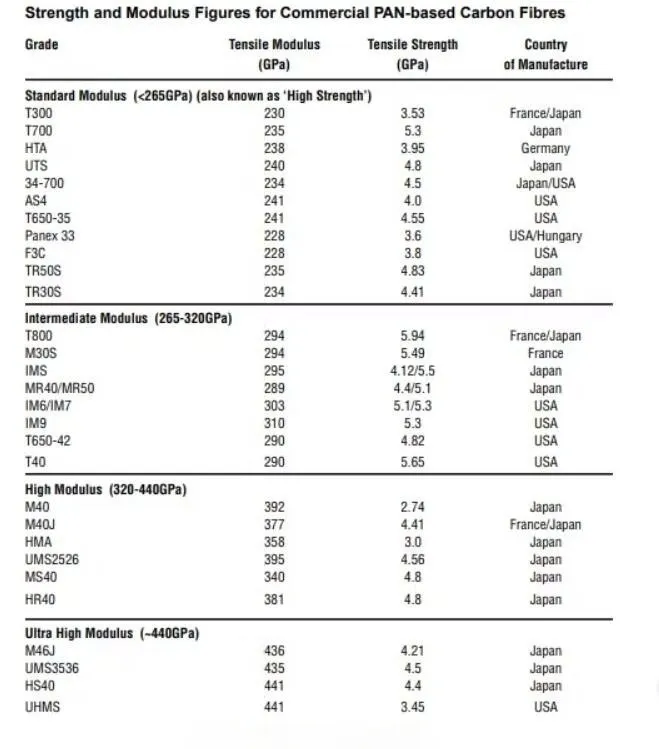
Applications of 3D Printed Carbon Fiber Molds
The versatility of 3D printed carbon fiber molds has led to their adoption across various industries:
- Aerospace Industry: 3D printed carbon fiber molds are ideal for creating lightweight, strong parts such as aircraft wings and fuselage sections.
- Automotive Industry: In automotive manufacturing, these molds are used to produce lightweight components for improved fuel efficiency and performance.
- Medical Devices: 3D printed molds allow for highly customized medical devices and implants with precise details.
- Consumer Goods: From electronics cases to sports equipment, these molds enable rapid production of durable, customized consumer goods.
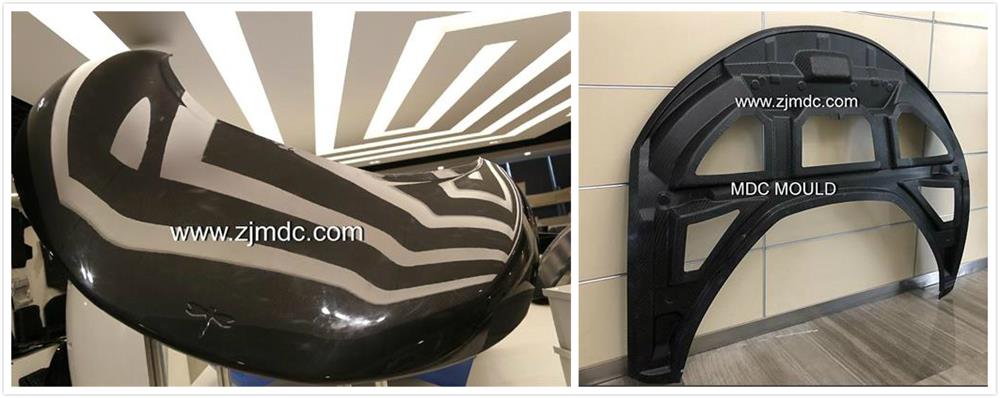
Challenges and Future Prospects of 3D Printed Carbon Fiber Molds
While the benefits are substantial, challenges remain, including the relatively high cost of carbon fiber filaments and the evolving technology for incorporating carbon fiber into 3D printing.
As 3D printing technology continues to improve, costs are expected to decrease, and more innovations will emerge. Future advancements may include multi-material 3D printing for even stronger molds and greater automation in manufacturing processes.
Conclusion
3D printed carbon fiber molds represent a significant advancement in manufacturing technology. Their speed, efficiency, and design flexibility make them valuable in industries from aerospace to automotive. As technology evolves, the applications for carbon fiber molds will continue to expand, offering businesses a competitive edge in modern manufacturing.
For those seeking fast, efficient production with high levels of customization, adopting 3D printed carbon fiber molds is a smart choice.