Composite materials, including those produced with SMC mold and BMC tooling, have emerged as game-changing solutions across various industries due to their unique properties, such as a high strength-to-weight ratio and anisotropic behavior. These characteristics have led to the increasing popularity and adoption of composites in industries like aerospace, automotive, marine, and sports equipment.

Introduction to Composite Materials and Processes
Composite materials, often crafted using processes such as SMC molding and GMT tooling, offer unique advantages due to their tailored strength and stiffness. These characteristics are achieved through strategic placement and orientation of fibers within the matrix, optimizing the material for specific performance requirements.
Laminate Composites
Laminate composites are continuous fiber composites where individual layers are oriented in a manner that enhances strength in the primary load-bearing direction. This method is often employed in SMC moulding and BMC molding to create high-performance components. Essentially, laminates consist of multiple layers of fibers arranged to optimize their strength and stiffness.
Fiber’s Key Role in Composites: Balancing Strength, Stiffness, and Durability
Fibers in composites play a critical role in providing strength and stiffness. Typically made from high-strength materials like carbon, glass, or aramid, fibers bear the majority of the load due to their superior strength and stiffness, while the polymer matrix binds them and facilitates load transfer between fibers. This is particularly evident in carbon fiber mold applications.
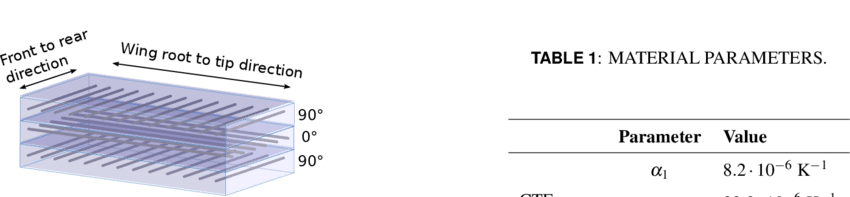
Matrix Material’s Fundamental Functions in Composites: Protection, Load Transfer, and Thermal Resistance
The matrix in composites serves several essential functions. It protects the fibers, maintains their proper alignment, and facilitates load transfer between them. Additionally, the matrix helps distribute compressive loads across all fibers in the composite, which is crucial in applications involving press molds and compression tooling.
Unique Materials and Processes
The unique properties of composites, such as a high strength-to-weight ratio and anisotropic behavior, significantly influence the design and engineering of composite components. Processes like thermoforming mold and SymaLITE mould are tailored to meet specific performance requirements by strategically placing and orienting fibers within the matrix.
Advantages of Composites
The use of composites, particularly those produced with LFT molding and D-LFT moulding, across various industries offers benefits like improved performance, weight reduction, and enhanced fuel efficiency. In aerospace, composites make aircraft structures lighter, leading to lower fuel consumption and emissions. In automotive, composites like those using hot compression mold and BMC moulding improve crashworthiness and vehicle performance.
Challenges Associated with Composite Manufacturing
Manufacturing composites presents its own set of challenges, including delamination, quality control, and the need for specialized tools and equipment such as thermoforming tooling and compression molds. To mitigate these challenges, careful design and planning, stringent quality control measures, and proper operator training and education are crucial.
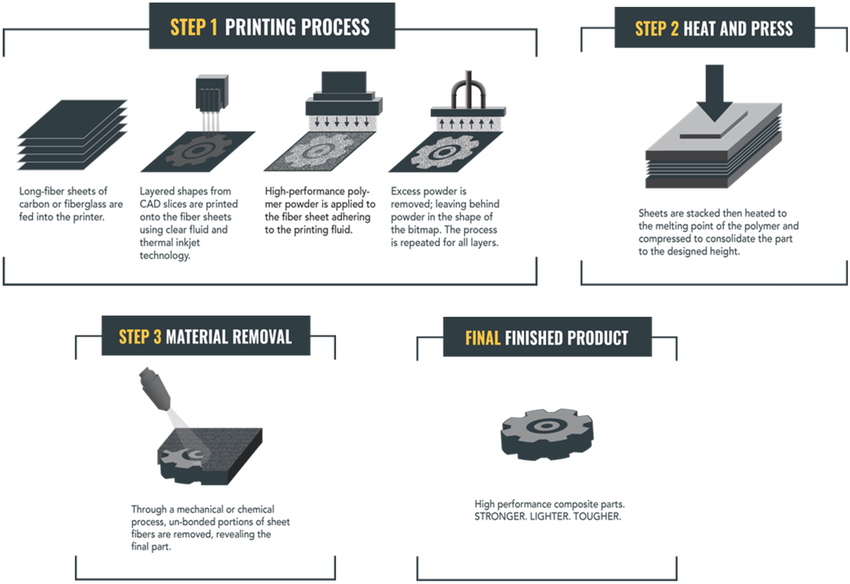
Conclusion
Understanding the unique properties of composites and their manufacturing processes, including those involving SMC tools and thermoset molds, is crucial for the successful design and engineering of composite components. By leveraging these unique materials and processes, industries can benefit from improved performance, weight reduction, and enhanced fuel efficiency. As the adoption of composites continues to rise, overcoming the challenges associated with manufacturing is essential to unlocking their full potential in various applications.