Carbon fiber is renowned for its exceptional strength-to-weight ratio, making it a preferred material in aerospace, automotive, and sports equipment industries. Laying carbon fiber in a mold requires meticulous attention to detail and a precise technique to ensure the final product meets the desired specifications. This guide will walk you through the process of , from preparation to finishing touches, ensuring your project is a success.
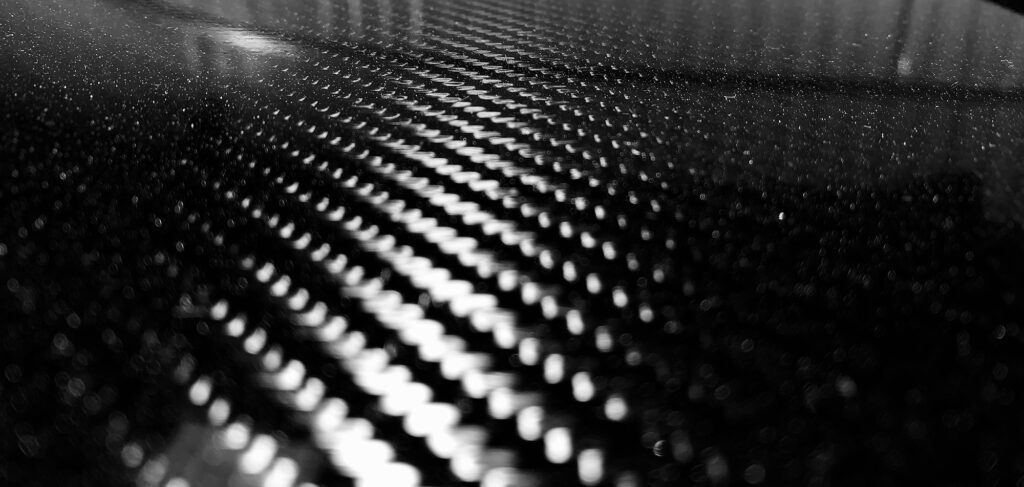
Preparation
Choose the Right Materials and Tools
- Carbon Fiber Fabric: Select the appropriate type and weave of carbon fiber fabric based on your project’s requirements.
- Resin System: Choose a compatible resin system (epoxy, polyester, or vinyl ester) that matches your carbon fiber and mold material.
- Mold: Ensure the mold is made from a material that can withstand the curing process, such as aluminum, steel, or high-temperature composite materials.
- Tools: Gather all necessary tools including brushes, rollers, scissors, protective gloves, and a vacuum bagging system if needed.
Prepare the Mold
- Cleaning: Clean the mold thoroughly to remove any dust, grease, or contaminants that could affect the bonding process.
- Release Agent: Apply a mold release agent to prevent the carbon fiber from sticking to the mold. Ensure an even coating for easy part removal.
Laying the Carbon Fiber
Cutting the Carbon Fiber Fabric
Measure and cut the carbon fiber fabric to fit the mold. Ensure precise cuts to minimize waste and overlaps. Cutting at a 45-degree angle to the weave can help in achieving better conformity to the mold’s shape.
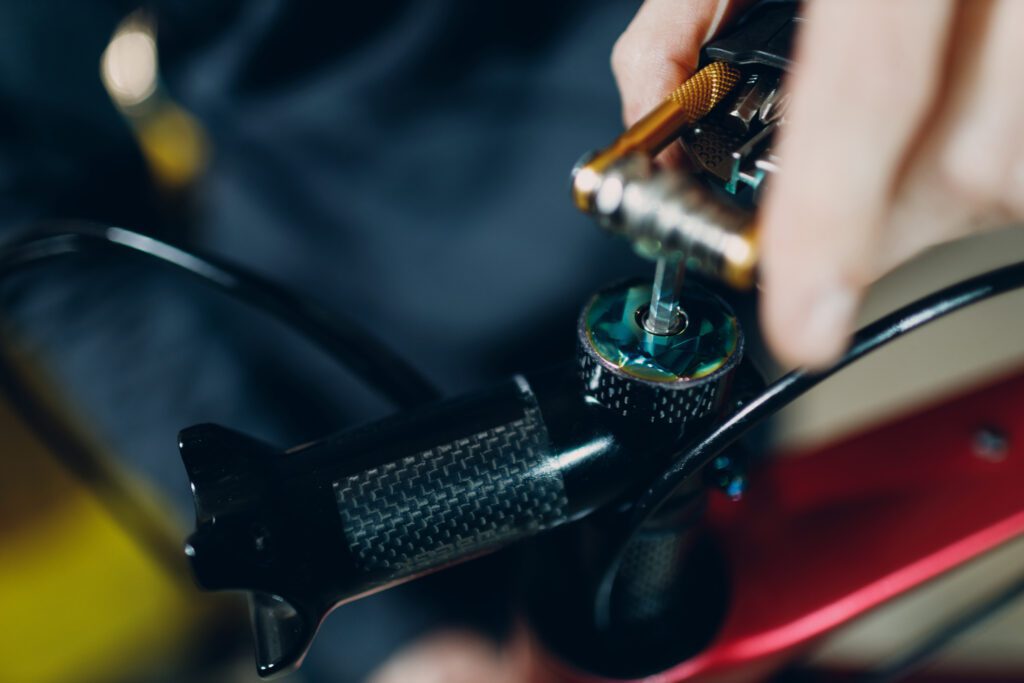
Applying the Resin
- Resin Mixing: Mix the resin and hardener according to the manufacturer’s instructions. Use a clean container and stir thoroughly to ensure an even mixture.
- Wet Layup: For wet layup techniques, apply a thin layer of resin on the mold surface using a brush or roller. Lay the first layer of carbon fiber fabric onto the resin-coated mold, then use a roller to impregnate the fabric with resin, ensuring all fibers are thoroughly saturated. Repeat the process for additional layers.
Vacuum Bagging (Optional)
For enhanced strength and a better finish, consider using a vacuum bagging system. Place a peel ply over the final layer of carbon fiber, followed by a perforated release film and a breather layer. Enclose the setup in a vacuum bag and use a vacuum pump to remove air and compress the layers, ensuring a void-free laminate.
Curing and Demolding
Curing
Allow the resin to cure according to the manufacturer’s specifications. This could range from room temperature curing to elevated temperature curing in an oven. Ensure the part remains undisturbed during this period to avoid defects.
Demolding
Once cured, carefully remove the vacuum bagging materials and peel ply. Gently separate the part from the mold using plastic wedges or demolding tools. Avoid using metal tools to prevent damaging the mold or the part.
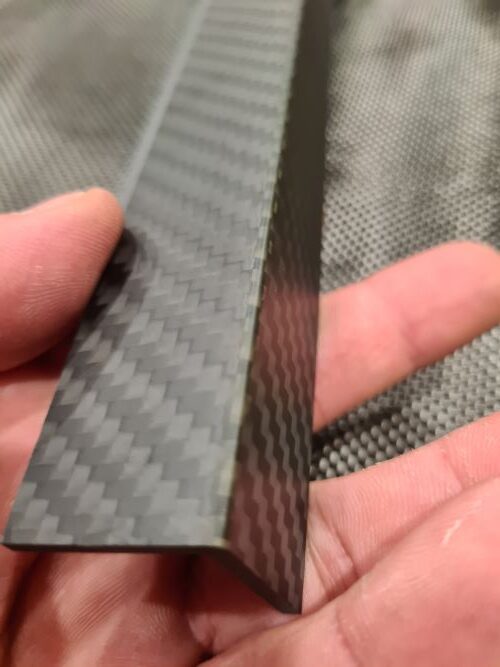
Finishing
Trimming and Sanding
Trim any excess material from the edges of the part using a rotary tool or diamond-tipped saw. Sand the edges to smooth out any rough areas and achieve the desired finish.
Final Inspection and Coating
Inspect the part for any defects or imperfections. If necessary, apply a clear coat or UV-protective layer to enhance the appearance and durability of the carbon fiber.
Tips for Success
- Maintain Cleanliness: Keep the workspace clean to avoid contamination of the carbon fiber and resin.
- Work in a Controlled Environment: Temperature and humidity can affect the curing process. Work in a controlled environment to achieve the best results.
- Follow Safety Protocols: Wear protective gear including gloves, masks, and safety glasses to protect against harmful chemicals and dust.