MDC Mould has been a pioneer in the field of compression moulding, offering cutting-edge solutions for SMC (Sheet Molding Compound) moulds, BMC (Bulk Molding Compound) moulds, and other related applications. This article explores the expertise of MDC Mould in compression moulding techniques, highlighting the significance of SMC moulds, BMC moulds, and advancements in this professional domain.
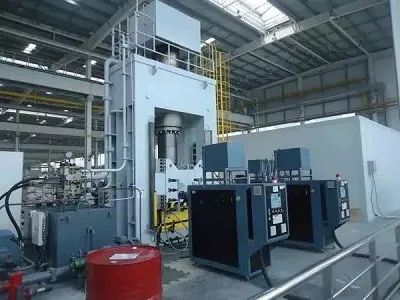
Understanding SMC Moulding and BMC Moulding:
SMC Moulding: SMC is a composite material composed of thermosetting resins, chopped glass fibers, and fillers. SMC moulding is widely used to create complex and durable parts with high strength-to-weight ratios, making it suitable for automotive, electrical, and construction industries.
BMC Moulding: BMC consists of a thermosetting resin, fillers, reinforcements, and additives. BMC moulding enables the production of intricate parts with excellent electrical insulation properties, flame resistance, and dimensional stability. It finds applications in electrical components, automotive parts, and more.
Benefits of Compression Moulding:
Compression moulding offers several advantages for SMC and BMC moulding processes, including:
High Precision: Compression moulding ensures accurate replication of intricate designs, resulting in consistent part dimensions and minimal post-processing requirements.
Material Flexibility: It allows the use of various composite materials, reinforcing fibers, and additives, providing versatility in achieving desired mechanical and electrical properties.
Cost-Effectiveness: Compression moulding offers efficient material usage, reduced scrap, and lower tooling costs compared to other moulding techniques.
Enhanced Mechanical Properties: The applied pressure during compression moulding ensures excellent fiber wet-out, leading to improved strength and structural integrity of the final parts.
Advanced Techniques in Compression Moulding:
MDC Mould utilizes advanced techniques to further enhance the quality and efficiency of compression moulding processes, such as:
Precision Tooling: MDC Mould employs state-of-the-art tooling technologies to create precise and durable SMC moulds, BMC moulds, and related tooling solutions.
Automated Production Systems: Leveraging automation and robotics, MDC Mould optimizes production processes, reduces cycle times, and ensures consistent part quality.
Simulation and Analysis: By employing simulation software and analysis tools, MDC Mould can optimize mould designs, material flow, and cooling systems to improve overall moulding efficiency.
Applications of Compression Moulded SMC and BMC Components:
Compression moulding finds widespread applications in various industries. Some common applications include:
Automotive: Bumpers, body panels, interior trims, and structural components.
Electrical and Electronics: Insulators, connectors, switches, and enclosures for electrical devices.
Construction: Composite building materials, electrical distribution boxes, and infrastructure components.
Consumer Goods: Appliance parts, bathroom fixtures, and furniture components.
MDC Mould stands at the forefront of compression moulding technology, offering exceptional expertise in SMC moulds, BMC moulds, and related applications. With their advancements in precision tooling, automation, and simulation techniques, they continue to drive innovation in the field. The versatility, precision, and cost-effectiveness of compression moulding make it a preferred choice for manufacturing high-quality components in various industries.
Neuroquiet review
Mitolyn
Nagano Lean Body Tonic review
Leanbiome
ProvaDent
LeanBiome
Lottery Defeater
Tonic greens review
Quietum plus
Nagano Lean Body Tonic
Mitolyn
Mytolyn review
Mitolyn
Alpha Bites
Lottery Defeater Review
Lottery Defeater Review
Boostaro review
Billionaire Brain Wave
Billionaire Brain Wave
Herpafend
Mitolyn review
Java burn
Mitolyn review
Mitolyn
Tea burn review
Mitolyn
Sight Care
Lottery Defeater review
Prodentim review
Prodentim
Boostaro
Lottery defeater review
Lottery defeater
Leanbiome review
Quietum Plus review
ZenCortex
Quietum Plus
Tonic Greens review
Provadent review
TonicGreens
Tonic Greens
Tonic Greens
Lottery Defeater
Lean Body Tonic
GlucoPure
Neuroquiet review
Neuroquiet
Java Burn
Mitolyn review
Leanbiome
ProDentim
Boostaro review
Boostaro
THE MONEY WAVE
Lottery defeater review
Nerve fresh review
Leanbiome review
Mitolyn
Zencortex review
NATURAL MOUNJARO
Zencortex
Zencortex review
Sight care
NANODEFENSE PRO
NANODEFENSE PRO REVIEW
Natural Mounjaro
NATURAL MOUNJARO RECIPE
Tonic Greens
Sight care review
Prodentim review
Lottery Defeater
TURMERIC TRICK
Mitolyn
NATURAL MOUNJARO RECIPE
Tonic Greens review
Sight care
Tonic Greens
Mitolyn
Lottery defeater
Boostaro
Natural Mounjaro recipe
Natural Mounjaro recipe
Sight care review
Java Burn review
Prodentim review
Prodentim review
Leanbiome review
Leanbiome review
Prodentim review
Zencortex
Sight care
Sight care
Nagano Lean Body Tonic
Lottery Defeater
NeuroQuiet review
Quietum Plus
Leanbiome review
Aqua Sculpt
Aqua Sculpt
Gluco Extend review
Prime Biome
NATURAL MOUNJARO
Gluco Tonic
Gluco Tonic
Sight care
Vertigenics review
Appanail review
Prodentim
Zencortex
Denticore
Nerve fresh review
Moringa magic
Boostaro
Lottery defeater review
Prodentim
Prodentim
Gluco6
Prodentim
Quietum plus review
LeanBiome
Prodentim
Prodentim review
Prodentim review
Lottochamp
Lotto champ
Prodentim
Appanail review
SALT TRICK RECIPE
Zencortez
Primebiome Review
Salt Trick
Nitric Boost
herpafend review
NERVEFRESH
Boostaro review
Lottery defeater
Fitspresso