As an important composite material mold, SMC mould is widely used in automobile, aerospace, electronics and other fields. Its production process requires strict control of parameters such as the size, shape, and position of the mold to ensure stable and consistent product quality. However, traditional measurement methods, such as manual measurement and traditional measuring instruments, have problems such as low measurement accuracy and low measurement efficiency, which are difficult to meet the requirements of SMC mold production. And advanced measuring equipment and instruments, such as Three coordinate measuring instrument, have been widely used in the production of SMC molds due to their high precision, high efficiency and multi-functional characteristics.
The basic principle and structure of CMM
The Coordinate Measuring Machine(CMM) is a measuring device based on a three-dimensional coordinate system. Its basic principle is to obtain the position and shape information of the object in the three-dimensional space by measuring the movement of the probe on the three coordinate axes, so as to realize the precise measurement of the object. and detection. A Coordinate Measuring Machine usually consists of a coordinate measuring system, a measuring probe, a workbench, a computer and related software.
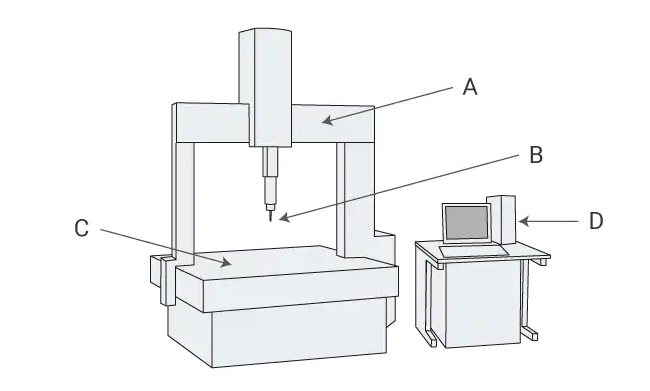
The coordinate measurement system is the core component of a Coordinate Measuring Machine, usually composed of three mutually perpendicular measurement axes and corresponding sensors, used to measure the position of the probe on the three coordinate axes. The measuring probe is the part that is in contact with the object to be measured. It can trigger the measurement action through the trigger, and transmit the measurement result to the computer for processing through the sensor. The workbench is used to place and fix the measured object, and usually has high-precision planes and fixtures to ensure the stability and accuracy of the measurement. The computer and related software are used to control the movement of the measuring instrument, process the measurement data, and generate measurement reports and data analysis.
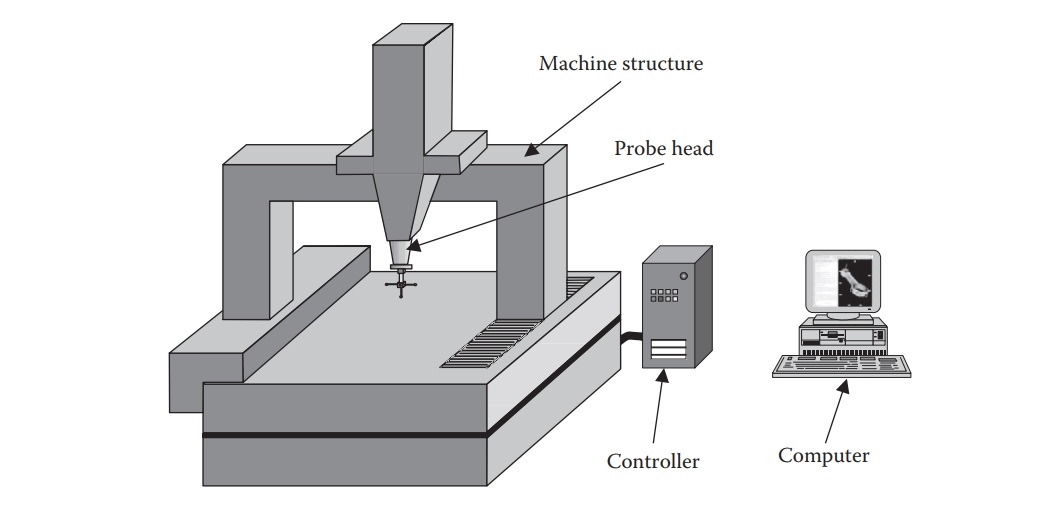
Features of CMM
Coordinate Measuring Machine has many advantages that make it one of the advanced measuring equipment.
- High precision: The Coordinate Measuring Machine adopts advanced sensor technology and measurement algorithm, and has a high degree of measurement accuracy, usually at the micron level. This enables it to meet the measurement requirements for high-precision products, especially in SMC molds, and can accurately measure parameters such as the size, shape and position of the mold.
- High efficiency: The Coordinate Measuring Machine has a fast measurement speed and an automated measurement process, which can greatly improve the measurement efficiency. At the same time, it can also realize the rapid detection and sorting of large batches of molds through the application of batch measurement and automatic measurement procedures, thereby improving production efficiency.
- Multifunctional: The Coordinate Measuring Machine can not only measure parameters such as size, shape and position, but also perform complex measurement tasks such as shape and position tolerance measurement, curved surface measurement, and contour measurement. At the same time, it can also perform data analysis, report generation, CAD comparison and other functions to help users conduct comprehensive quality control and data analysis.
- Non-contact measurement: The Coordinate Measuring Machine usually adopts a non-contact measurement method to avoid contact with the measured object, thereby avoiding measurement errors and damage to the object. This is especially important for SMC molds that require high surface quality, and can ensure the integrity and quality of the mold.
Application of CMM in SMC mould
CMM is widely used and important in SMC mold production. The following are its main applications in SMC mold production:
- Mold size measurement: The Coordinate Measuring Machine can quickly and accurately measure the size of the SMC mold, including parameters such as length, width, height, and diameter. This is very important to ensure that the size of the mold meets the design requirements and ensure the accuracy and consistency of the product.
- Mold shape measurement: The Coordinate Measuring Machine can measure the complex shape of the SMC mold, including surface shape, contour shape, etc. It can realize comprehensive and accurate measurement of the shape of the mold through high-precision sensors and measurement algorithms to ensure that the shape of the mold meets the design requirements.
- Mold position measurement: The Coordinate Measuring Machine can measure the position of the mold in three-dimensional space, including the position, posture and relative position of the mold. This is very important to ensure the positioning accuracy of the mold, the matching accuracy of adjacent parts, and the assembly and disassembly of the mold.
- Shape and position tolerance measurement: SMC molds usually need to meet certain shape and position tolerance requirements to ensure the assembly and use performance of the product. The Coordinate Measuring Machine can measure the shape and position tolerance, including parallelism, perpendicularity, position tolerance, angle tolerance, etc., to help ensure that the shape and position tolerance of the mold meets the design requirements.
- Mold quality control: The Coordinate Measuring Machine can carry out comprehensive quality control on SMC molds. Through the analysis and comparison of measurement data, it can judge whether the mold is qualified, provide measurement reports and data analysis, and help manufacturers find and solve molds in time. Quality issues, to ensure the quality stability and consistency of the mold.
- Mold improvement and optimization: CMM can also be used for mold improvement and optimization. By analyzing the measurement data of the mold, the existing problems and potential improvement space of the mold can be found out, and a scientific basis can be provided for the optimal design and production of the mold.
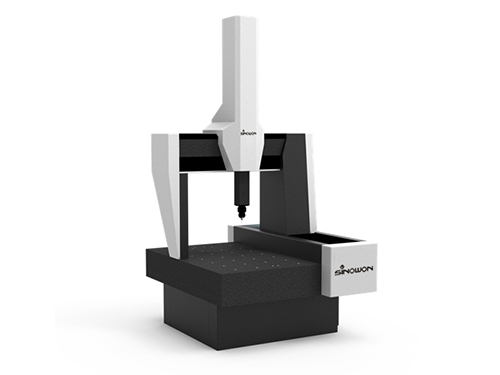
To sum up, the Coordinate Measuring Machine has important application value in the production of SMC molds, which can ensure the accurate measurement and quality control of parameters such as the size, shape, position and geometric tolerance of the mold, and help manufacturers improve product quality and reduce reduce production costs and improve production efficiency.
As a professional SMC mould manufacturer, MDC Mould have a lot of equipment and measuring and testing instruments continuous improvement. We have purchased advanced measuring equipment and instruments such as imported Coordinate Measuring Machine, which allow us to understand the quality situation of each product, process, and standard, and provide the best service for our quality control department. Our QC department will conduct product inspection and submit test report within 24 hours after mold test. The report will include comprehensive testing and analysis on product size, appearance, injection technology and physical parameters. We use different inspection standards and tools for different products. In our laboratory, we have carried out different tests on high pressure injection, high speed injection, clamping time, etc. The quality control department proposes modification and improvement suggestions for unqualified products. We have accumulated rich experience and applied it in mold production to provide customers with good solutions.
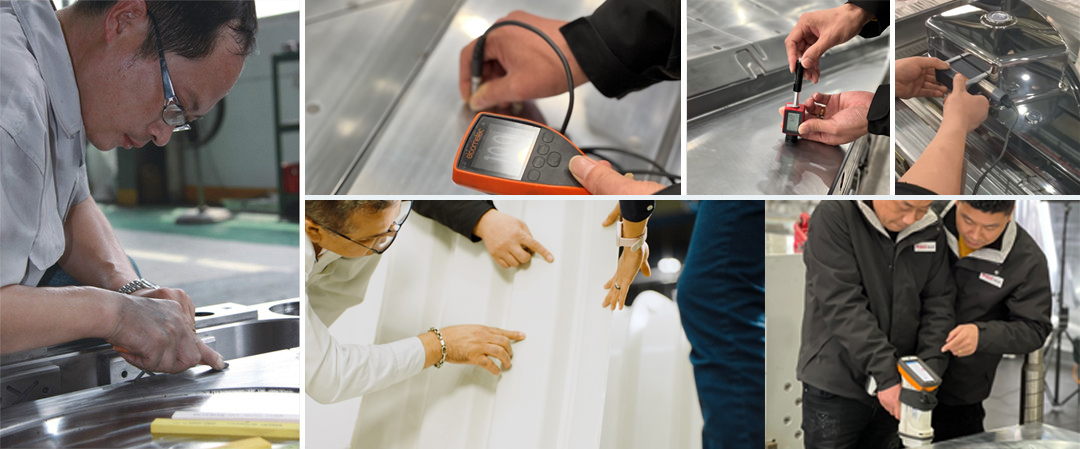